Why Properly Torque Bolts
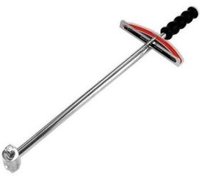
Professional mechanics, driveway mechanics and most people that work on cars hate taking the time to torque bolts properly. As a professional mechanic myself I don’t like it either. First you have to break out your torque wrench and maybe even get it calibrated.
Next you have to find the actual torque specification in an online car repair manual for the bolt that you are going to tighten. Then you’ll have to take extra care and get your torque wrench on the bolt and finally torque it to specification. This is a lot of effort when you can just put a wrench on that very same bolt and just pull on it for two grunts and a groan.
Not applying proper bolt torque would be considered a shortcut that can reduce the quality of the car repair and may cause a repeat failure or additional repairs to be performed. This is more critical in some areas such as intake manifold bolts. If these are not torqued properly they can allow coolant to run inside the engine and damage expensive internal parts.
Add to this the fact that many modern aluminum intakes now use composite gaskets that are primarily made of plastic and this increases the necessity for proper bolt torque. On some of these modern aluminum intake manifolds the actual torque specification is very low and the pattern that you tighten the bolts down in is extremely critical.
Why do we have to torque bolts
All metals whether they are aluminum, steel or even titanium have some elastic properties to them. This property means the bolt can be stretched and compressed. When the bolt is stretched a clamping force or holding power is created due to the bolts natural tendency to want to return to its original length. This can stop the bolt from backing off even if it is exposed to lots of vibration.
Like a spring the more bolts are stretched the tighter it becomes. Keep in mind that a bolt can be stretched too far. When you have gone past this point of no return you can often feel it in the wrench. When you reached this point the pressure applied to the wrench turns the bolt further with less effort. This is your telltale sign that you have gone way too far.
Often this is when the head snaps off and leaves an extremely tight bolt with no head stuck in a hole. When this happens the repair time is increased greatly along with the troubles that may be generated by drilling and removing the broken bolt.
When you compare the amount of aggravation generated by breaking a bolt compared to the time that it would take to look up the proper torque specification and set up your torque wrench you are much better off doing it the right way.
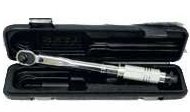
After being a mechanic for 25 years most often I would use my half-inch torque wrench. But now it seems that I use my 3/8 drive torque wrench even more. I have also recently had to add an inch pound torque wrench to my tool-set.
This has been an ongoing trend of bolts that are torque to a lighter specification. The good news is the cost of these tools has continued to come down. Visit my auto facts website for more information about torquing bolts and access to inexpensive bolt torque wrenches.
For more of the latest posts to this website you can get back to the homepage from this next link. I add new articles about once a week to the auto repair information blog.